Addressing Challenges In Automated Visual Inspection Of Lyophilized Vials
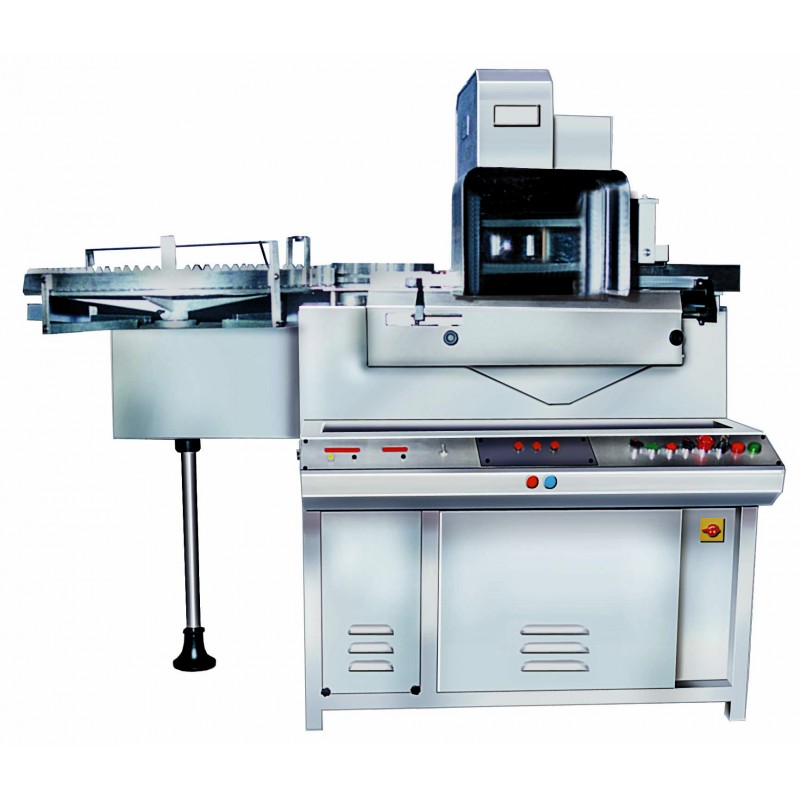
Table of Contents
Challenges Related to Lyophilization Process Variability
The lyophilization process itself introduces inherent variability that significantly impacts the effectiveness of automated visual inspection. Understanding and addressing this variability is crucial for reliable defect detection.
Variations in Cake Appearance
Lyophilized drug cakes exhibit a wide range of appearances depending on factors such as formulation, freezing rate, and drying conditions. These variations can include cracks, fissures, collapse, and inconsistencies in surface texture.
- Inconsistent cake appearance makes automated defect recognition difficult. Algorithms must be trained to differentiate between acceptable variations and actual defects.
- Sophisticated image analysis algorithms are required. These algorithms need to account for the natural variability in cake morphology and identify only critical defects. This often requires advanced techniques like machine learning and deep learning.
- Calibration and training data must account for this variability. A comprehensive dataset encompassing a wide range of acceptable and unacceptable cake appearances is essential for effective algorithm training. This dataset should include images captured under various lighting conditions to account for variations in illumination.
Sublimation and Residual Moisture
The sublimation process, where ice transforms directly into vapor, can leave behind residual moisture or create imperfections that might be misinterpreted as defects by the automated inspection system.
- Accurate detection requires precise control of lighting and image acquisition parameters. Careful control of illumination minimizes shadows and reflections which can mask subtle defects or create artifacts.
- Advanced image processing techniques, such as moisture mapping, can help. These techniques allow for the identification and quantification of residual moisture, distinguishing it from other defects.
- Robust algorithms are needed to differentiate between harmless moisture and actual defects. The algorithm needs to be trained to recognize the subtle differences in appearance between acceptable moisture levels and problematic levels that indicate a potential quality issue.
Challenges in Automated Image Acquisition and Processing
Even with consistent lyophilization, achieving accurate automated visual inspection presents significant challenges related to image acquisition and processing.
High-Throughput Requirements
Pharmaceutical production lines demand high-speed automated inspection systems to maintain production rates. This speed requirement adds complexity to the challenge.
- Balancing speed with accuracy is crucial. High-speed imaging can compromise image quality, leading to missed defects or false positives.
- High-performance cameras and processing units are necessary. These components enable rapid image capture and analysis while maintaining sufficient resolution and sensitivity.
- Optimization of image acquisition protocols is critical to minimize inspection time. This involves careful selection of camera settings, lighting conditions, and image processing algorithms.
Lighting and Image Artifacts
Variations in lighting conditions, reflections, and shadows can create artifacts that interfere with accurate defect detection.
- Precise lighting control, such as diffuse lighting, is essential. Uniform illumination minimizes shadows and reflections, improving image quality.
- Advanced algorithms for noise reduction and artifact removal are needed. These algorithms help to filter out unwanted artifacts and enhance the visibility of actual defects.
- Careful calibration of the imaging system is vital. This ensures consistent lighting and image acquisition across all inspections.
Defect Classification and False Positives
Distinguishing between minor variations and actual critical defects is a major challenge requiring sophisticated algorithms. Minimizing false positives is critical to avoid unnecessary rejection of good vials.
- Machine learning techniques can significantly improve defect classification. These techniques can learn to identify subtle patterns and features that are indicative of defects.
- Careful training of algorithms with diverse datasets is vital. The training dataset must include a wide variety of vial images, representing the full range of acceptable and unacceptable variations.
- Minimizing false positives is critical to avoid unnecessary rejection of good vials. This reduces waste and improves overall efficiency.
Addressing the Challenges: Technological Advancements and Solutions
Several technological advancements offer promising solutions to overcome the challenges in automated visual inspection of lyophilized vials.
Advanced Image Processing Techniques
The application of Artificial Intelligence (AI), machine learning (ML), and deep learning (DL) is revolutionizing automated defect detection. These techniques enable the development of sophisticated algorithms capable of analyzing complex images and identifying subtle defects with greater accuracy than traditional methods.
Improved Lighting and Imaging Systems
Specialized lighting systems, such as those employing structured lighting or polarized light, significantly improve the visibility of defects. High-resolution cameras with advanced sensors provide detailed images, facilitating more accurate defect identification.
Data Analytics and Process Optimization
Data analytics plays a vital role in refining the automated visual inspection process. By analyzing inspection data, manufacturers can identify trends, optimize inspection parameters, and continuously improve the accuracy and efficiency of their systems.
Conclusion
Automated visual inspection of lyophilized vials presents significant challenges related to process variability, image acquisition, and defect classification. However, advancements in image processing techniques, lighting systems, and machine learning offer powerful solutions. By addressing these challenges effectively, the pharmaceutical industry can ensure consistent quality control, reduce production costs, and improve overall efficiency in lyophilized vial inspection. Investing in robust and reliable automated visual inspection systems is crucial for maintaining high standards in pharmaceutical manufacturing. Consider exploring the latest advancements in automated visual inspection of lyophilized vials to optimize your quality control processes and enhance product safety.
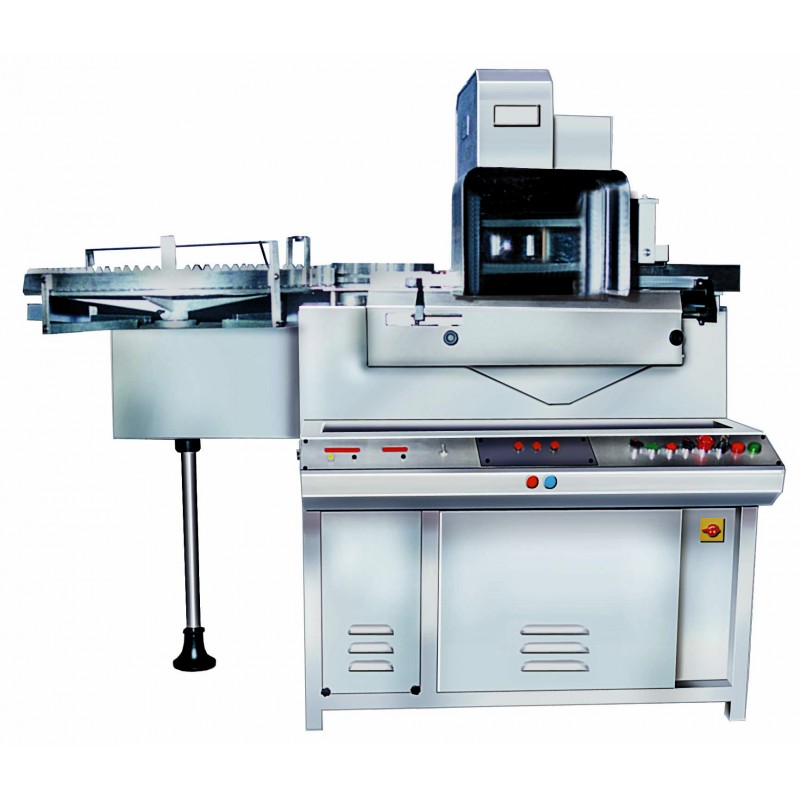
Featured Posts
-
The Devastating Effects Of The Gaza Blockade Hunger Sickness And Crime
May 11, 2025 -
Sylvester Stallone Et Moi L Histoire Derriere L Exposition
May 11, 2025 -
Payton Pritchard Crowned Sixth Man Of The Year
May 11, 2025 -
Zurich Classic Mc Ilroy Lowry Team Confirmed For Title Defense
May 11, 2025 -
Averea Lui Sylvester Stallone Cat A Adus Rocky
May 11, 2025
Latest Posts
-
Sylvester Stallone Reveals His Favorite Rocky Film An Emotional Rollercoaster
May 12, 2025 -
Which Rocky Movie Touches Sylvester Stallone The Most Exploring The Franchises Emotional Core
May 12, 2025 -
The Most Emotional Rocky Movie According To Sylvester Stallone A Critical Analysis
May 12, 2025 -
Sylvester Stallone Picks His Top Rocky Film Why This One Is So Emotional
May 12, 2025 -
Exploring Sylvester Stallones Only Non Starring Directorial Effort
May 12, 2025