Addressing Quality Control Issues In Automated Lyophilized Vial Inspection
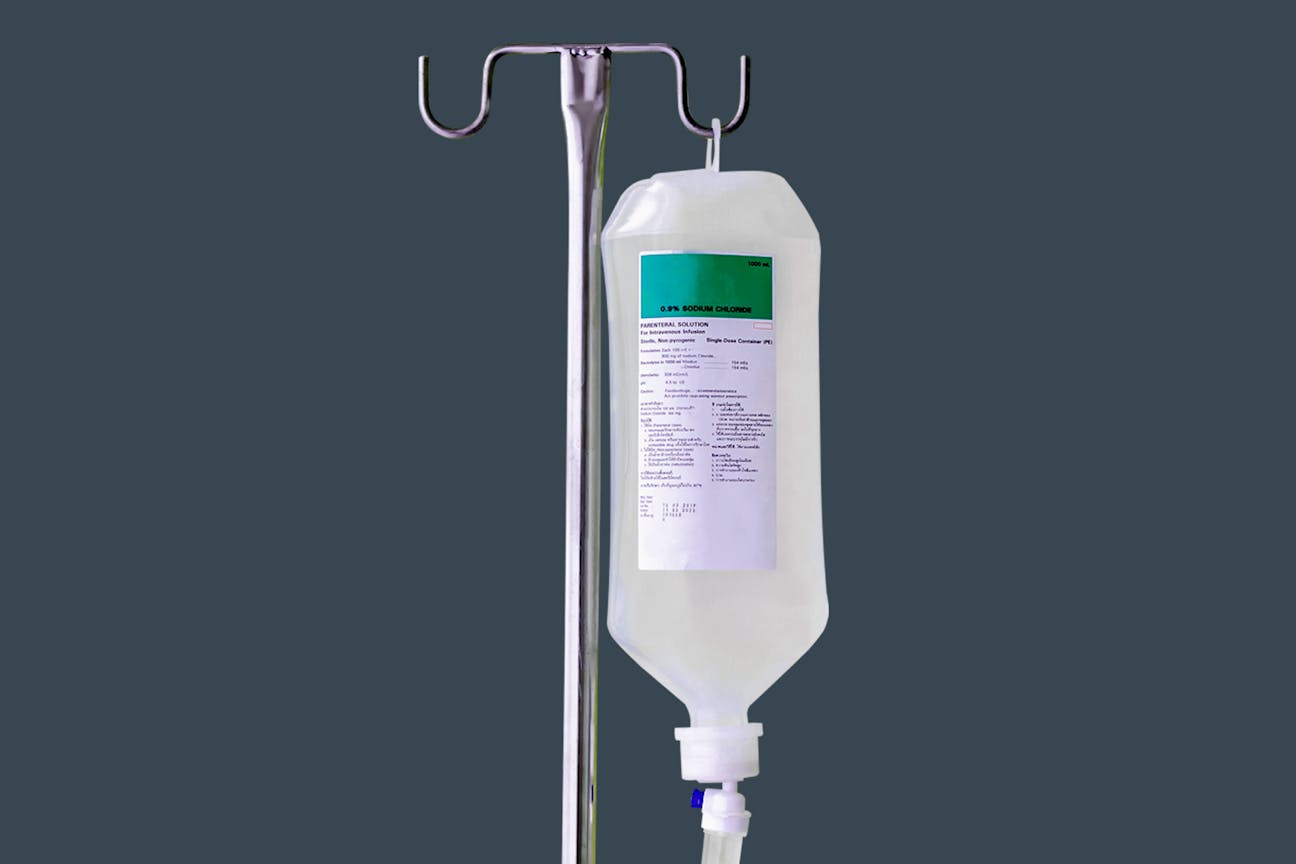
Table of Contents
Identifying Common Defects in Lyophilized Vials
Automated lyophilized vial inspection systems must be capable of identifying a range of defects. Failing to detect even minor flaws can compromise product integrity and patient safety. Common defects include:
- Cracks and chips in the vial: These structural imperfections can lead to leakage, contamination, and drug degradation. Automated vision systems often utilize image analysis algorithms to detect these subtle cracks.
- Particulate matter within the vial: Foreign particles, however small, can be detrimental to the drug's quality and potentially harmful to patients. Laser-based detection methods are commonly employed to identify particulate contamination.
- Fill level inconsistencies: Variations in fill levels can indicate inconsistencies in the lyophilization process or potential dosage errors. Precise measurement techniques, often integrated within automated systems, are essential for consistent fill level verification.
- Cap seal failures: Improperly sealed vials are susceptible to contamination and degradation. Automated systems can use image analysis to assess the integrity of the cap seal, ensuring airtight closure.
- Vial damage (e.g., scratches, deformations): Scratches or deformations can compromise the vial's structural integrity, potentially leading to leakage. Advanced vision systems with high-resolution imaging capabilities are vital for detecting such damage.
Detecting these defects reliably is paramount. Advanced inspection techniques, such as high-resolution vision systems and laser-based particle counters, play a crucial role in achieving high accuracy. The selection of appropriate inspection methods depends heavily on the specific types of defects that are most likely to occur.
Optimizing Automated Lyophilized Vial Inspection Systems
Optimizing automated lyophilized vial inspection systems is crucial for maximizing accuracy and minimizing errors. Several key factors contribute to optimal performance:
- System Calibration and Validation: Regular calibration using standardized test vials and documented procedures is essential. This ensures the system consistently meets performance specifications.
- Regular calibration schedules should be established and strictly adhered to.
- Standardized test vials with known defects should be used for validation purposes.
- Meticulous documentation of all calibration and validation activities is critical for compliance and traceability.
- Image Processing Algorithms: Sophisticated image processing algorithms are the heart of automated inspection systems. Advancements in AI and machine learning significantly improve defect detection accuracy.
- AI and machine learning algorithms can adapt and learn, enhancing their ability to identify subtle defects.
- Challenges remain in dealing with variations in vial appearance (e.g., color, clarity) and lighting conditions.
- Algorithm optimization and ongoing training with diverse datasets are vital for maintaining accuracy.
- Lighting and Camera Positioning: Proper lighting and precise camera positioning are critical for capturing high-quality images. Optimal illumination minimizes shadows and reflections that can obscure defects.
Implementing Effective Quality Control Measures
Effective quality control goes beyond the automated system itself. Several crucial measures must be implemented:
- Statistical Process Control (SPC): SPC techniques, such as control charts, allow for continuous monitoring of the automated system's performance, identifying trends and potential problems early.
- Setting appropriate control limits is essential for effective monitoring.
- Regular analysis of control charts helps identify deviations from expected performance.
- Prompt corrective actions are necessary whenever trends or deviations are detected.
- Human Oversight: While automation significantly improves efficiency, human oversight remains crucial. Visual verification of flagged vials ensures the accuracy of automated detection and reduces false positives.
- Clear protocols should be established for human intervention and decision-making.
- Personnel should receive comprehensive training on proper inspection techniques and decision-making processes.
- Detailed Records and Documentation: Maintaining detailed records, including batch numbers, vial identification, and inspection results, is essential for traceability and compliance. This information is vital for investigating potential issues and improving processes.
Troubleshooting and Addressing Inspection Failures
Despite optimization efforts, inspection system failures can occur. Understanding common causes and effective troubleshooting strategies is essential:
- Common Causes of Failures:
- Hardware issues such as camera malfunctions, lighting problems, and mechanical failures.
- Software glitches including algorithm errors, software bugs, and communication errors.
- Troubleshooting and Resolution: A proactive approach to preventative maintenance, including regular servicing and component replacement, minimizes downtime. Robust diagnostic tools can help pinpoint the source of failures.
- Quality Management System (QMS): A well-defined QMS ensures that inspection failures are addressed effectively, documented thoroughly, and prevent recurrence.
Ensuring Quality in Automated Lyophilized Vial Inspection
Effective quality control in automated lyophilized vial inspection requires a multi-faceted approach. By implementing the strategies outlined above—optimizing systems, employing rigorous quality control measures, and proactively addressing failures—pharmaceutical manufacturers can significantly improve the accuracy and efficiency of their inspection processes. Automated systems play a vital role in ensuring product quality and patient safety in lyophilized vial production. Proactive implementation of these quality control measures is not simply a regulatory requirement; it is a commitment to patient safety and the production of high-quality pharmaceuticals. We encourage you to adopt these best practices to enhance the accuracy and efficiency of your automated lyophilized vial inspection processes. The long-term benefits of proactive quality control in automated lyophilized vial inspection are undeniable.
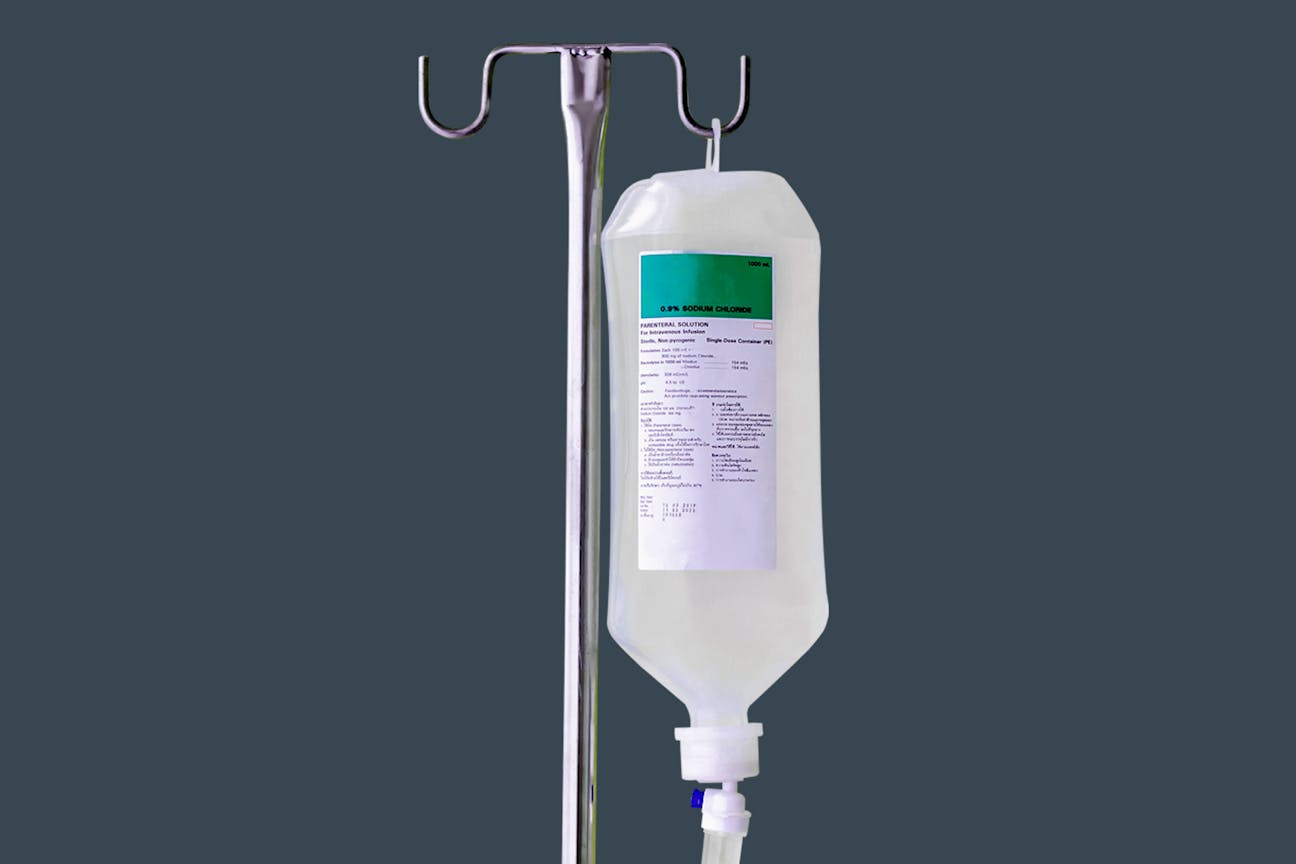
Featured Posts
-
Moscows Red Square Putins Display Of Power At Victory Day Parade
May 12, 2025 -
Le Duo Explosif Chantal Ladesou Se Confie Sans Filtre Sur Ines Reg Mask Singer
May 12, 2025 -
Nba Award Boston Celtics Guard Declines Campaign
May 12, 2025 -
New Cooyah Grand Slam Track Collection A Closer Look
May 12, 2025 -
Crazy Rich Asians Tv Series Henry Goldings Insights Into Cast Reunions
May 12, 2025
Latest Posts
-
Mtv Movie And Tv Awards Cancelled For 2025 Official Confirmation
May 12, 2025 -
Jessica Simpsons Daughter Birdie 6 Matches Mom In Cute Yellow Swimsuits
May 12, 2025 -
Analyzing The Vma Simulcast On Cbs A Threat To Mtvs Relevance
May 12, 2025 -
The Impact Of Cbss Vma Simulcast On Mtvs Viewership
May 12, 2025 -
Airport Fashion Jessica Simpsons Cheetah Print And Blue Fur Ensemble
May 12, 2025