Automated Visual Inspection Of Lyophilized Vials: A Focus On Quality Control Challenges
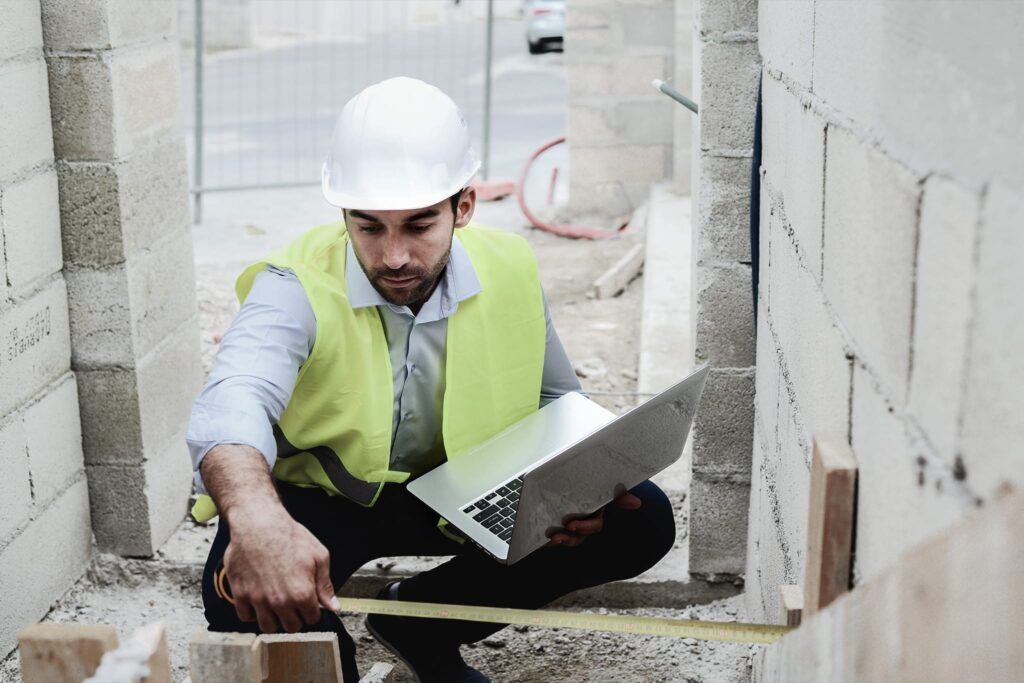
Table of Contents
1. Introduction
The demand for efficient and reliable quality control in pharmaceutical manufacturing is at an all-time high. This is particularly true for lyophilized products, which require meticulous inspection to ensure product integrity and patient safety. Manual visual inspection of lyophilized vials, the traditional approach, presents significant challenges. Speed limitations, inconsistent results due to human error, and the difficulty in detecting subtle defects all contribute to significant risks. Automated Visual Inspection of Lyophilized Vials offers a powerful solution, promising improved efficiency, enhanced accuracy, and ultimately, higher product quality.
2. Main Points
H2: Challenges in Manual Visual Inspection of Lyophilized Vials
H3: Subjective Assessment and Inter-Operator Variability
Manual inspection relies heavily on the subjective judgment of individual inspectors. This leads to significant inter-operator variability, causing inconsistencies in defect detection.
- Variations in interpretation of defects like particulate matter (size, type, location), cracks (size, location, severity), and discoloration (intensity, uniformity) are common.
- These inconsistencies directly impact product quality, potentially leading to the release of substandard products and non-compliance with stringent regulatory requirements, like those stipulated by the FDA.
H3: Bottlenecks in Production and Increased Costs
Manual visual inspection is a time-consuming process, creating significant bottlenecks in production lines. This translates to increased labor costs and extended lead times.
- Automated systems can offer significant cost savings. A typical manual inspection line might process 100 vials per hour, while an automated system could easily handle 500-1000 vials per hour, resulting in substantial cost reductions.
- A comparison of manual versus automated throughput reveals a dramatic increase in efficiency, potentially reducing labor costs by 50% or more, depending on the scale of production.
H3: Difficulty in Detecting Subtle Defects
The human eye has limitations, particularly when it comes to identifying small or subtle defects in lyophilized vials.
- Minute cracks, internal particulate matter, and variations in fill level can easily be missed during manual inspection.
- These subtle defects can compromise product safety and efficacy, leading to potential health risks for patients and significant financial repercussions for manufacturers.
H2: Advantages of Automated Visual Inspection Systems
H3: Enhanced Speed and Throughput
Automated visual inspection systems drastically increase inspection speed and throughput.
- Automated systems can inspect thousands of vials per hour, significantly improving production efficiency. Specific throughput rates will vary depending on the system and configuration.
- This increased speed translates to faster time-to-market, allowing companies to meet increased demand and gain a competitive advantage.
H3: Improved Accuracy and Consistency
Automation eliminates human error, resulting in significantly improved accuracy and consistency in defect detection.
- Automated systems consistently detect defects, minimizing both false positives (incorrectly identifying a defect) and false negatives (missing a defect).
- The increased reliability and repeatability of inspection results ensure higher product quality and greater confidence in regulatory compliance.
H3: Objective Data and Traceability
Automated systems generate objective data and comprehensive audit trails, fulfilling regulatory requirements.
- Detailed inspection reports, including images of detected defects and timestamps, facilitate thorough data management and reporting.
- This ensures enhanced compliance with regulations such as 21 CFR Part 11, vital for pharmaceutical manufacturing.
H3: Advanced Imaging Techniques
Automated systems utilize various advanced imaging techniques for superior defect detection.
- High-resolution cameras capture detailed images, while spectral imaging analyzes the light reflected from the vials to identify subtle variations in composition or structure.
- These technologies significantly improve the sensitivity and specificity of defect detection, ensuring that even the most subtle flaws are identified.
H2: Implementing Automated Visual Inspection: Key Considerations
H3: System Selection and Validation
Choosing the right system and validation are crucial steps in implementing automated visual inspection.
- Factors to consider include throughput requirements, resolution, the types of defects to be detected, and ease of integration with existing equipment.
- Thorough system validation, according to industry standards and regulatory requirements (e.g., FDA guidelines), is essential to ensure the accuracy and reliability of the system.
H3: Integration with Existing Production Lines
Integration with existing production lines requires careful planning and execution.
- Considerations include physical space, data transfer protocols, and operator training.
- Potential challenges can be addressed through careful planning, collaboration with experienced integrators, and thorough testing.
H3: Data Analysis and Interpretation
Efficient data analysis and interpretation are crucial for process improvement.
- Sophisticated data analysis tools can help identify trends and patterns in defect detection, enabling proactive problem-solving.
- Using data for process optimization and continuous improvement leads to further quality enhancements and cost reductions.
3. Conclusion
Manual visual inspection of lyophilized vials is hampered by subjectivity, inconsistency, and limited throughput. Automated Visual Inspection of Lyophilized Vials, however, offers a compelling solution, providing significantly improved speed, accuracy, and consistency. The benefits include reduced costs, enhanced quality control, and better regulatory compliance. By embracing automated systems and utilizing advanced imaging techniques, pharmaceutical manufacturers can significantly improve their quality control processes and enhance patient safety. To explore available solutions for Automated Visual Inspection of Lyophilized Vials and optimize your quality control strategies, we encourage you to research the latest technologies and contact industry experts for consultation. Implementing automated visual inspection is a significant step towards a more efficient and reliable pharmaceutical manufacturing process.
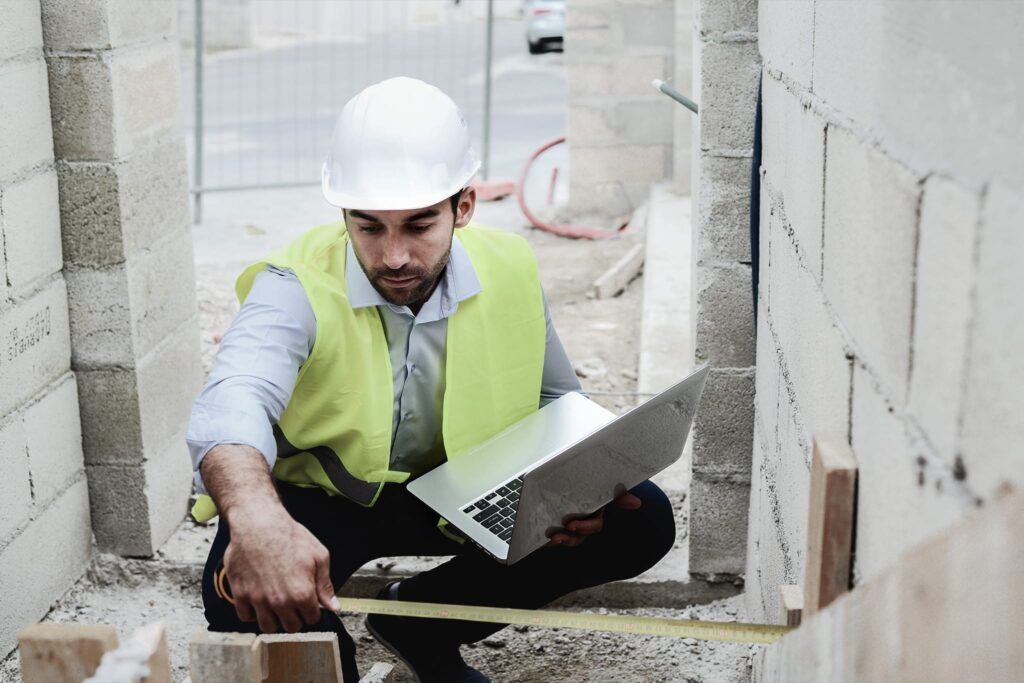
Featured Posts
-
Bctv Daily Dispatch Superman Daredevil Vs Bullseye And 1923 News
May 12, 2025 -
The End Of An Era Thomas Muellers Final Match At The Allianz Arena
May 12, 2025 -
Parliamentary Pressure Mounts Action Needed On Undocumented Workers
May 12, 2025 -
Ipswich Town Women Target Victory Against Gwalia To Secure League Lead
May 12, 2025 -
Grand Slam Victory Jamaica Observer Coverage
May 12, 2025
Latest Posts
-
Sylvester Stallone Reveals His Favorite Rocky Film An Emotional Rollercoaster
May 12, 2025 -
Which Rocky Movie Touches Sylvester Stallone The Most Exploring The Franchises Emotional Core
May 12, 2025 -
The Most Emotional Rocky Movie According To Sylvester Stallone A Critical Analysis
May 12, 2025 -
Sylvester Stallone Picks His Top Rocky Film Why This One Is So Emotional
May 12, 2025 -
Exploring Sylvester Stallones Only Non Starring Directorial Effort
May 12, 2025