Challenges And Advancements In Automated Visual Inspection Of Lyophilized Products
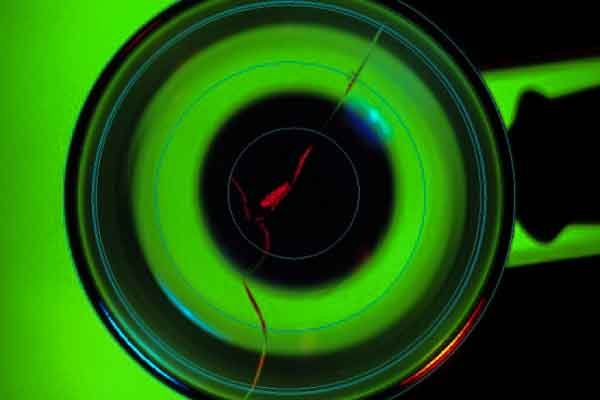
Table of Contents
Challenges in Automated Visual Inspection of Lyophilized Products
Implementing automated visual inspection systems for lyophilized products isn't without its difficulties. Several key challenges need to be addressed for successful implementation and reliable performance.
Variations in Lyophilized Product Appearance
Lyophilized products exhibit inherent variability in their appearance due to several factors. The freeze-drying process itself, along with formulation nuances and container variations, can lead to a range of visual characteristics. This inherent variability makes consistent automated defect detection particularly challenging.
- Examples of visual defects: Cracks, fissures, collapse, uneven surfaces, discoloration, particulate matter, and foreign bodies.
- Difficulties in setting consistent thresholds: Defining clear thresholds to differentiate between acceptable variations and actual defects requires careful consideration and robust algorithms, accounting for the natural variations in lyophilized cakes. This is crucial to avoid false positives and ensure accurate defect detection. Inconsistencies in lighting or camera angle can further exacerbate these challenges in automated defect detection. The complexity of lyophilization defects makes accurate visual inspection essential.
Keywords: Lyophilization defects, visual inspection challenges, automated defect detection, lyophilization visual inspection
Difficulties in Image Acquisition and Processing
Obtaining high-quality images of lyophilized products suitable for automated analysis presents significant technical hurdles. The subtle nature of many defects, coupled with the inherent challenges of imaging translucent or semi-transparent products, requires sophisticated image acquisition techniques.
- Challenges in image acquisition: Controlling lighting to minimize shadows and reflections is crucial. Variations in vial shape and position can also affect image quality and consistency. The need for high-resolution imaging is vital for detecting subtle defects.
- Image processing complexities: Variations in color, texture, and contrast within a single vial, or between vials, demand robust image processing algorithms. These algorithms need to effectively differentiate between acceptable variations in appearance and actual defects, ensuring that only true defects trigger alerts.
- Imaging Technologies: Visible light imaging is commonly used, but advanced techniques like near-infrared (NIR) imaging offer potential advantages in certain cases. However, each technology has its limitations and specific applications.
Keywords: Image processing, lyophilization image analysis, automated image analysis, high-resolution imaging, NIR imaging, visible light imaging
Validation and Regulatory Compliance
Automated visual inspection systems used in pharmaceutical manufacturing must adhere to stringent regulatory requirements to ensure accuracy, reliability, and data integrity. This necessitates comprehensive validation processes.
- Validation protocols: Rigorous testing is necessary to demonstrate the system's ability to consistently detect defects with high accuracy and low false positive rates. This includes evaluating the system's performance across different batches, operators, and environmental conditions.
- Regulatory guidelines: Compliance with regulatory guidelines from agencies like the FDA (Food and Drug Administration) and EMA (European Medicines Agency) is paramount. These guidelines outline specific requirements for validation, documentation, and ongoing performance monitoring of automated systems.
- Performance qualification: Demonstrating that the system consistently meets predefined performance criteria is essential for regulatory approval and ongoing compliance. This involves ongoing monitoring and maintenance of the equipment and software.
Keywords: Validation of automated visual inspection, GMP compliance, regulatory requirements, lyophilization quality control
Advancements in Automated Visual Inspection of Lyophilized Products
Despite the challenges, significant advancements are driving improvements in the accuracy, efficiency, and reliability of automated visual inspection for lyophilized products.
Improved Imaging Technologies
Recent advancements in imaging technologies are enhancing the capabilities of automated visual inspection systems.
- Hyperspectral and multispectral imaging: These advanced techniques capture images across a wide range of wavelengths, providing significantly richer data than traditional visible light imaging. This allows for better differentiation between subtle defects and normal variations in appearance, improving the accuracy of defect detection. Spectral analysis allows identification of defects based on their unique spectral signatures.
- Improved resolution: Higher resolution cameras capture finer details, improving the detection of small or subtle defects that might be missed by lower-resolution systems.
Keywords: Hyperspectral imaging in lyophilization, multispectral imaging, advanced imaging techniques, automated visual inspection systems
Sophisticated Image Analysis Algorithms
The development of sophisticated image analysis algorithms is crucial for improving the accuracy and robustness of automated visual inspection.
- AI-powered algorithms: Machine learning (ML) and deep learning (DL) algorithms, particularly convolutional neural networks (CNNs), are increasingly used to analyze images and identify defects with greater accuracy than traditional methods. These algorithms learn from large datasets of images, allowing them to recognize complex patterns and subtle variations.
- Algorithm performance metrics: The performance of these algorithms is evaluated using metrics such as precision, recall, and F1-score, ensuring high accuracy and minimizing false positives and negatives. Large, high-quality training datasets are crucial to the success of these AI-powered methods.
Keywords: AI-powered visual inspection, machine learning in lyophilization, deep learning for defect detection, image analysis algorithms
Integration with Manufacturing Execution Systems (MES)
Integrating automated visual inspection systems with Manufacturing Execution Systems (MES) offers significant benefits for overall process optimization and quality control.
- Real-time data analysis: Integration enables real-time analysis of inspection data, providing immediate feedback on product quality. This allows for rapid identification and correction of any issues in the lyophilization process.
- Process monitoring and control: Real-time data facilitates continuous monitoring of the lyophilization process, enabling proactive adjustments to optimize process parameters and improve yield.
- Improved traceability: Integration enhances traceability by linking inspection data to specific batches and production parameters.
Keywords: MES integration, automated visual inspection data, process automation, lyophilization process control
Conclusion
Automated visual inspection of lyophilized products is a crucial element in maintaining product quality and ensuring compliance with regulatory standards. While challenges related to image acquisition, algorithm development, and validation remain, significant advancements in imaging technologies, AI-powered algorithms, and system integration are driving improvements in accuracy, efficiency, and reliability. By embracing these advancements, the pharmaceutical industry can enhance the quality control of lyophilized products, improve overall manufacturing efficiency, and minimize production downtime. To stay at the forefront of this rapidly evolving field, continued investment in research and development of automated visual inspection of lyophilized products is essential.
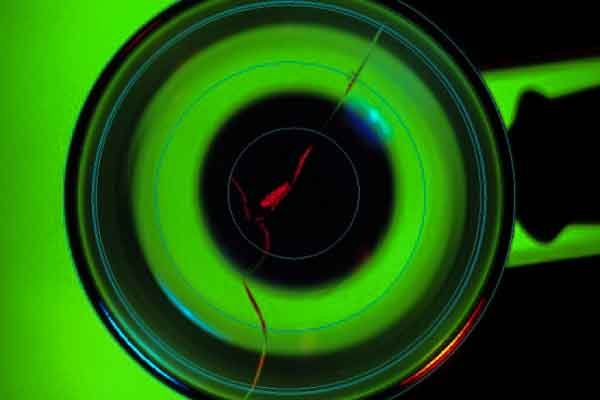
Featured Posts
-
Celtics Clinch Division After Magic Blowout Win
May 11, 2025 -
Jessica Simpsons New Song Hints Of Eric Johnson Infidelity
May 11, 2025 -
Karlyn Pickens Record Breaking 78 2 Mph Pitch A New Era In Ncaa Softball
May 11, 2025 -
Philippe Candeloro Et Chantal Ladesou Participent A La Vente Des Vins De Nuits Saint Georges
May 11, 2025 -
Nba Sixth Man Of The Year Payton Pritchards Unexpected Victory
May 11, 2025
Latest Posts
-
Boris Dzhonson Kritikuet Mirniy Plan Trampa Analiz Situatsii
May 12, 2025 -
Valspar Championship Lowry Makes A Push For The Title
May 12, 2025 -
Voyna V Ukraine Dzhonson Osuzhdaet Mirniy Plan Trampa
May 12, 2025 -
Reaccion De Boris Johnson Ante Ataque De Avestruz En Texas
May 12, 2025 -
Plan Trampa Po Mirnym Peregovoram Kritika So Storony Borisa Dzhonsona
May 12, 2025