Challenges And Advancements In Automated Visual Inspection Systems For Lyophilized Vials
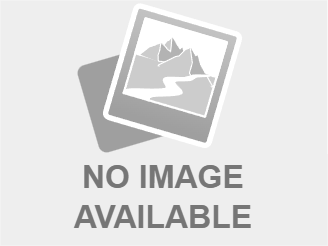
Table of Contents
Challenges in Automated Visual Inspection of Lyophilized Vials
Automated visual inspection offers significant advantages over manual methods, increasing efficiency and reducing human error. However, the unique characteristics of lyophilized vials present several challenges:
Difficulties in Detecting Defects
Lyophilized vials present a complex visual landscape. Detecting subtle defects requires sophisticated technology. The inherent nature of the lyophilization process, along with the delicate nature of the product, contributes to the complexity.
- Hairline cracks: These minute fractures are difficult to identify due to their size and often subtle appearance.
- Small particulates: Identifying and classifying foreign particles within the vial requires high-resolution imaging and advanced algorithms.
- Variations in cake appearance: The lyophilized cake's visual characteristics can vary significantly due to differences in the lyophilization process, making defect detection challenging. Light scattering further complicates the process, masking subtle imperfections.
Dealing with Variations in Lyophilized Products
Variations in the lyophilization process introduce inconsistencies in product appearance. These variations, while sometimes acceptable, can be difficult to distinguish from actual defects. Factors such as temperature fluctuations, pressure changes, and cycle variations during the freeze-drying process significantly influence the final product's visual characteristics.
- Temperature inconsistencies: Uneven temperature distribution during freezing can lead to variations in cake density and appearance.
- Pressure fluctuations: Changes in pressure during sublimation can affect the cake's structure and introduce visual inconsistencies.
- Cycle time variations: Variations in cycle duration can influence the final cake structure and appearance, potentially impacting automated inspection results.
High Throughput Requirements and Speed Limitations
Pharmaceutical manufacturing requires high throughput. Automated visual inspection systems must keep pace with production demands. Balancing speed and accuracy remains a significant challenge. Faster inspection systems may compromise accuracy, while excessively cautious systems may fail to meet production targets.
- Throughput bottlenecks: Slower inspection rates can create bottlenecks in the production line, leading to delays and reduced efficiency.
- System limitations: Some automated systems struggle to maintain accuracy at high throughput rates, leading to false positives or false negatives.
- System Optimization: Constant optimization of imaging parameters, algorithms, and hardware is crucial to achieve the required balance between speed and accuracy.
Cost and Implementation Challenges
Implementing automated visual inspection systems involves significant upfront investment. The cost encompasses not only the hardware and software but also the integration with existing production lines and the specialized training required for operation and maintenance. Return on investment (ROI) is a major consideration, requiring careful planning and assessment.
- Hardware costs: High-resolution cameras, advanced lighting systems, and robust robotic handling systems constitute a significant portion of the initial investment.
- Software costs: Advanced image processing algorithms and AI-powered defect classification software add to the overall cost.
- Integration costs: Integrating the system with existing manufacturing infrastructure and quality control systems requires significant effort and expertise.
Advancements in Automated Visual Inspection Systems for Lyophilized Vials
Significant advancements are addressing the challenges outlined above. The industry is witnessing a rapid evolution in automated visual inspection technology for lyophilized vials:
Improved Imaging Techniques
The adoption of advanced imaging technologies significantly enhances defect detection capabilities.
- High-resolution cameras: These cameras capture minute details, improving the detection of hairline cracks and small particulates.
- Multispectral imaging: This technique uses various wavelengths of light to capture more detailed information about the vial's contents, enhancing the detection of subtle defects.
- 3D imaging: 3D imaging provides a comprehensive view of the vial and its contents, allowing for the detection of defects that may be missed by 2D imaging.
Advanced Image Processing and AI
Artificial intelligence (AI) and machine learning (ML) are revolutionizing automated visual inspection.
- AI-powered defect classification: AI algorithms are used to classify defects with greater accuracy and speed than traditional methods.
- Pattern recognition: AI can identify subtle patterns and anomalies that may indicate the presence of defects.
- Anomaly detection: AI systems can learn to identify deviations from expected patterns, flagging potentially problematic vials.
Integration with other technologies
Integrating automated visual inspection systems with other quality control technologies improves overall efficiency and product quality.
- Weight checking: Automated weight verification ensures the vial contains the correct amount of product.
- Leak detection: Integrated leak detection systems verify the integrity of the vial seal.
- Data analytics: Integration with data analytics platforms allows for real-time monitoring and trend analysis, enabling proactive quality control.
Conclusion: The Future of Automated Visual Inspection for Lyophilized Vials
The challenges associated with automated visual inspection of lyophilized vials are significant, but advancements in imaging technology, AI, and integration strategies are paving the way for more efficient and accurate systems. The future of Automated Visual Inspection Systems for Lyophilized Vials lies in continued innovation, leading to improved accuracy, increased throughput, and enhanced compliance with stringent regulatory requirements. Investing in advanced automated visual inspection systems is crucial for ensuring the quality and safety of lyophilized pharmaceuticals. Explore the latest advancements in automated vial inspection and take a step toward enhancing your quality control processes. The benefits of improved accuracy, efficiency, and compliance are undeniable.
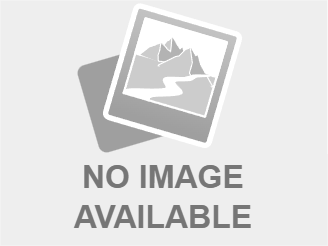
Featured Posts
-
Valentina Shevchenkos Dragon Themed Ufc Apparel A Closer Look
May 12, 2025 -
Close Call Knicks Secure Second Straight Overtime Win Against Bulls
May 12, 2025 -
Plan Trampa Po Mirnym Peregovoram Kritika So Storony Borisa Dzhonsona
May 12, 2025 -
Rahal Letterman Lanigan Racings 2025 Indy Car Season Prospects
May 12, 2025 -
Why Apples Choices Benefit Google More Than You Think
May 12, 2025
Latest Posts
-
The Future Of Mtv After The Cbs Vma Simulcast
May 12, 2025 -
Vma Simulcast On Cbs Did Mtv Lose Its Grip On Music Awards
May 12, 2025 -
Mtv Movie And Tv Awards Cancelled For 2025 Official Confirmation
May 12, 2025 -
Jessica Simpsons Daughter Birdie 6 Matches Mom In Cute Yellow Swimsuits
May 12, 2025 -
Analyzing The Vma Simulcast On Cbs A Threat To Mtvs Relevance
May 12, 2025