Enhancing Automated Visual Inspection Of Lyophilized Vials: A Comprehensive Review
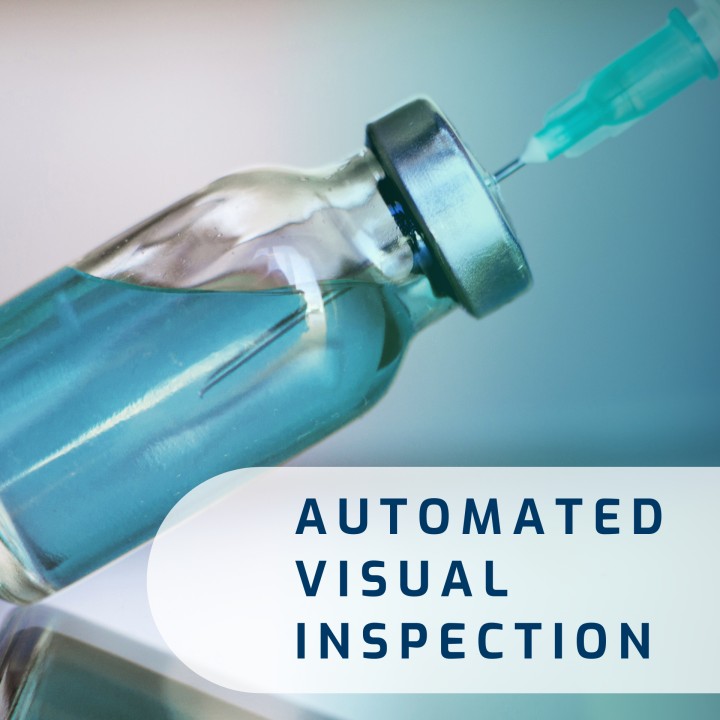
Table of Contents
Challenges in Manual Inspection of Lyophilized Vials
Manual visual inspection of lyophilized vials presents several significant challenges that impact both product quality and production efficiency.
Subjectivity and Variability
Manual inspection is inherently subjective. The interpretation of defects can vary significantly between inspectors, leading to inconsistencies and the potential for overlooking critical defects.
- High variability in human performance: Individual inspectors have different levels of experience, training, and attention to detail, resulting in inconsistent inspection results.
- Increased risk of human error: Fatigue, distraction, and even slight variations in lighting can lead to missed defects or false positives.
- Difficulty in maintaining consistent inspection standards: Ensuring consistent inspection standards across different shifts and personnel is challenging, leading to potential quality issues.
Throughput Limitations
Manual inspection is a slow process, creating a significant bottleneck in high-volume pharmaceutical production lines.
- Bottlenecks in production: Manual inspection can significantly delay the overall production process, impacting delivery schedules.
- Increased lead times: The slow pace of manual inspection extends the time required to bring products to market.
- Higher labor costs: The labor-intensive nature of manual inspection contributes to higher overall production costs.
Ergonomic Concerns
Prolonged manual inspection tasks can lead to operator fatigue, repetitive strain injuries, and other ergonomic issues.
- Increased risk of workplace injuries: Repetitive movements and strained postures during manual inspection increase the risk of musculoskeletal disorders.
- Reduced worker productivity: Fatigue and discomfort reduce the efficiency and accuracy of inspectors.
- Higher healthcare costs: Workplace injuries associated with manual inspection can lead to increased healthcare expenses for both the employee and the company.
Technologies for Automated Visual Inspection of Lyophilized Vials
Automated visual inspection systems utilize advanced technologies to overcome the limitations of manual inspection.
Image Acquisition Techniques
High-quality image acquisition is crucial for accurate defect detection. This involves employing high-resolution cameras and sophisticated lighting techniques.
- Different camera types and their suitability for various defect detection: Cameras with varying resolutions and sensitivities are selected based on the specific types of defects being targeted (e.g., particulate matter, cracks, discoloration).
- Importance of lighting optimization for different defect types: Different lighting techniques, such as brightfield, darkfield, and polarized light, are employed to enhance the visibility of different types of defects in lyophilized vials.
Image Processing and Analysis
Advanced algorithms and AI-powered solutions are essential for analyzing the acquired images and automatically identifying defects.
- Machine learning algorithms for defect classification: Machine learning models are trained on large datasets of vial images to classify various types of defects with high accuracy.
- Computer vision techniques for identifying cracks, particulate matter, and other defects: Computer vision algorithms are used to detect subtle variations in the vial's appearance, such as cracks, particulate matter, and variations in fill level.
Robotic Systems for Automated Handling
Robotic systems automate the handling and presentation of vials to the inspection system, improving efficiency and reducing the risk of damage.
- Increased throughput: Robotic systems significantly increase the number of vials that can be inspected per unit of time.
- Reduced risk of damage during handling: Automated handling minimizes the risk of vials being damaged during the inspection process.
- Improved overall efficiency: Automation streamlines the entire inspection process, leading to improved overall efficiency and reduced production downtime.
Benefits of Automated Visual Inspection
The transition from manual to automated visual inspection offers substantial benefits for pharmaceutical manufacturers.
Improved Accuracy and Consistency
Automated systems provide significantly higher accuracy and consistency compared to manual inspection.
- Reduced false positives and false negatives: Automated systems minimize the risk of both missing real defects and incorrectly identifying non-defective vials.
- Improved detection rates for subtle defects: Automated systems can detect subtle defects that may be missed by human inspectors.
Increased Throughput and Efficiency
Automation dramatically increases the speed of inspection, leading to improved production throughput and reduced lead times.
- Higher production capacity: Automated systems enable manufacturers to inspect a significantly larger number of vials in a given timeframe.
- Faster turnaround times: Automated inspection reduces the time required to complete quality control checks, accelerating the overall production process.
- Reduced operational costs: While initial investment costs are higher, automated systems often lead to significant long-term cost savings through increased efficiency and reduced labor costs.
Enhanced Data Management and Traceability
Automated systems capture detailed data on each vial inspected, improving traceability and enabling comprehensive quality control reporting.
- Better compliance with regulatory requirements: Detailed data logs and traceability features help pharmaceutical companies meet stringent regulatory requirements.
- Improved data analysis capabilities: The vast amounts of data generated by automated systems enable detailed analysis of defect trends and patterns, facilitating process improvements.
- Easier identification of defect trends: Automated systems can identify recurring defects, allowing manufacturers to address root causes and prevent future quality issues.
Future Trends in Automated Visual Inspection of Lyophilized Vials
The field of automated visual inspection is constantly evolving, with several exciting trends shaping its future.
Integration with other technologies
Future systems will likely integrate automated visual inspection with other quality control methods.
- Streamlined workflows: Integrating various inspection methods reduces handling steps and streamlines workflows, improving overall efficiency.
- Reduced processing time: Combining different inspection methods in a single integrated system reduces the overall processing time.
- Improved overall quality control: A holistic approach to quality control provides a more comprehensive assessment of product quality.
Advancements in AI and Machine Learning
Ongoing advancements in AI and machine learning will further enhance the accuracy and capabilities of automated visual inspection systems.
- Improved sensitivity and specificity of defect detection: More sophisticated algorithms will allow for the detection of increasingly subtle defects.
- Potential for predictive maintenance: AI can be used to predict potential equipment failures, minimizing downtime and ensuring continuous operation.
Miniaturization and increased flexibility
Smaller, more flexible inspection systems will allow for greater adaptability to diverse vial formats and production line configurations.
- Increased adaptability: Smaller systems are more easily integrated into existing production lines and can accommodate a wider range of vial sizes and shapes.
- Reduced footprint: Miniaturization reduces the physical space required for the inspection system.
- Lower cost of implementation: Smaller, more modular systems may offer lower initial investment costs.
Conclusion
Automated visual inspection represents a substantial leap forward in quality control for lyophilized vials. By overcoming the limitations of manual inspection, these systems deliver enhanced accuracy, consistency, efficiency, and data management capabilities. The future of automated visual inspection is promising, with ongoing advancements in AI, robotics, and integration technologies paving the way for even greater improvements in speed, accuracy, and flexibility. Investing in advanced automated visual inspection systems for your lyophilized vials is crucial for maintaining the highest product quality, meeting regulatory compliance, and achieving optimal production efficiency. Learn more about how to enhance your automated visual inspection of lyophilized vials today!
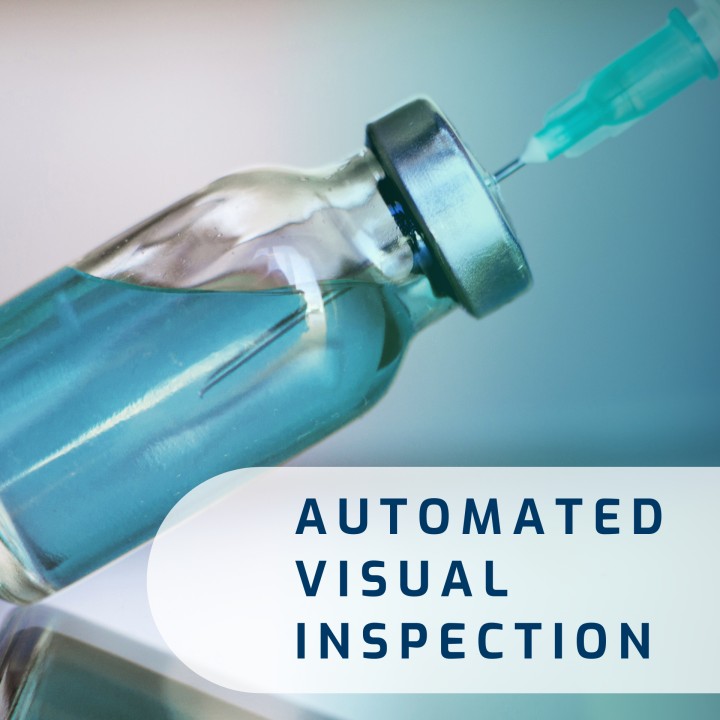
Featured Posts
-
Chaplin And Victory Key Moments For Ipswich Town
May 12, 2025 -
Senior Calendar Of Events Trips Outings And Social Gatherings
May 12, 2025 -
Nemecka Futbalova Legenda Thomas Mueller Sa Luci S Bayernom Mnichov
May 12, 2025 -
Virginia Giuffres Beskyldninger Konsekvenser For Prins Andrew Og Kongefamilien
May 12, 2025 -
Tom Hanks And Tom Cruises Unsettled 1 Debt The Story Behind The Joke
May 12, 2025
Latest Posts
-
Future Of Mtv Movie And Tv Awards Uncertain After 2025 Cancellation
May 12, 2025 -
2025 Mtv Movie And Tv Awards Officially Cancelled
May 12, 2025 -
The Future Of Mtv After The Cbs Vma Simulcast
May 12, 2025 -
Vma Simulcast On Cbs Did Mtv Lose Its Grip On Music Awards
May 12, 2025 -
Mtv Movie And Tv Awards Cancelled For 2025 Official Confirmation
May 12, 2025