How U.S. Companies Are Responding To Tariff Uncertainty: A Cost-Cutting Focus
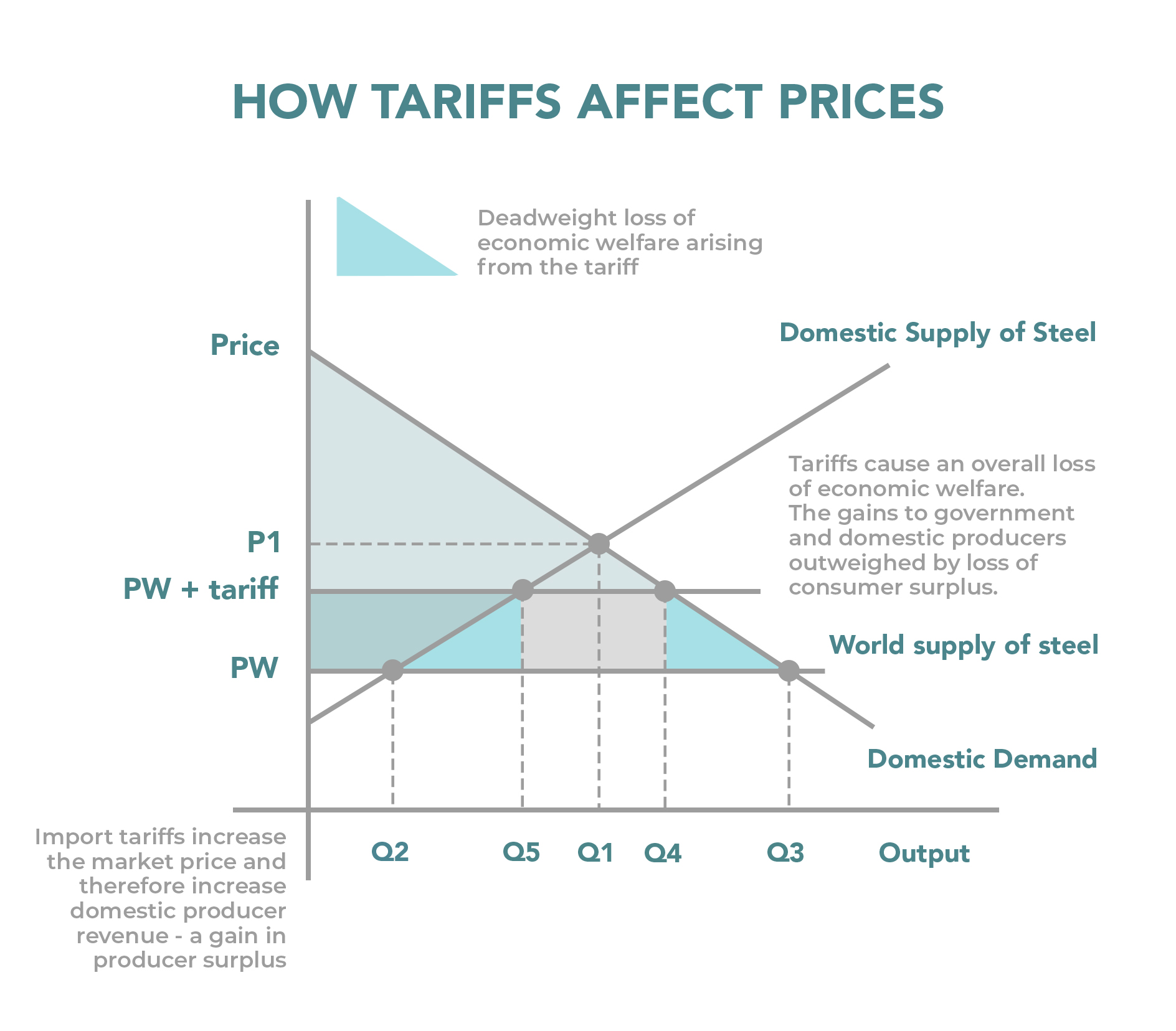
Table of Contents
Restructuring Supply Chains to Minimize Tariff Impacts
The imposition of tariffs has dramatically reshaped supply chains, prompting businesses to seek strategies to mitigate the increased costs.
Sourcing from Alternative Countries:
Many companies are diversifying their sourcing strategies, moving production away from countries subject to high tariffs. This involves a complex evaluation of factors like:
- Examples: Relocating manufacturing from China to Vietnam, Mexico, or other Southeast Asian nations.
- Challenges: Navigating different regulatory environments, adapting to varying labor costs and skillsets, and the potential for longer lead times.
- Impact: This shift can improve resilience against future tariff changes but also presents logistical and operational challenges.
Nearshoring and Regionalization:
To reduce reliance on distant suppliers and mitigate the risks associated with long supply chains, many companies are embracing nearshoring. This involves relocating production to countries geographically closer to the U.S., such as Mexico or Canada.
- Examples: Companies in the automotive and electronics industries are increasingly using nearshoring to shorten supply chains.
- Advantages: Reduced shipping costs, quicker delivery times, and improved responsiveness to market demands.
- Disadvantages: Potentially higher labor costs compared to offshore manufacturing. However, these costs can be offset by reduced transportation expenses and faster production cycles. This also supports domestic job creation.
Investing in Automation and Technology:
To boost efficiency and offset increased labor costs stemming from tariffs, companies are investing heavily in automation and technology.
- Examples: Adopting robotics in manufacturing, implementing advanced analytics for inventory management, and utilizing AI-powered supply chain optimization tools.
- ROI Considerations: The initial investment in automation can be substantial. However, long-term cost savings through increased productivity and reduced labor expenses often justify the expense.
- Impact on Employment: While automation may lead to job displacement in some areas, it also creates new opportunities in technology and maintenance roles.
Implementing Cost-Cutting Measures Across Operations
Beyond supply chain restructuring, U.S. companies are actively implementing cost-cutting measures across their operations.
Reducing Operational Expenses:
Businesses are scrutinizing every aspect of their operations to identify areas for cost reduction. This includes:
- Renegotiating supplier contracts: Securing better pricing and payment terms with vendors.
- Optimizing logistics: Implementing more efficient transportation and warehousing strategies.
- Improving energy efficiency: Reducing energy consumption through upgrades and technological improvements.
- Lean manufacturing principles: Streamlining production processes to eliminate waste and improve efficiency.
Workforce Optimization:
Navigating tariff uncertainty often necessitates adjustments to workforce strategies. While companies strive to maintain a strong workforce, this might include:
- Hiring freezes: Restricting new hires to control labor costs.
- Attrition management: Carefully managing employee turnover to minimize recruitment and training expenses.
- Strategic restructuring: Reorganizing departments and teams to improve efficiency and reduce redundancy. Ethical considerations regarding layoffs and employee well-being are paramount.
Inventory Management Strategies:
Effectively managing inventory is critical during periods of tariff uncertainty. Companies are adapting their strategies to minimize the impact of fluctuating costs:
- Just-in-Time (JIT) inventory: Reducing inventory levels to minimize storage costs and the risk of obsolescence due to tariff changes.
- Predictive analytics: Utilizing data-driven insights to accurately forecast demand and optimize stock levels.
- Challenges: Maintaining adequate inventory levels while mitigating the financial risks associated with fluctuating tariff costs and demand uncertainty.
Lobbying and Advocacy Efforts to Influence Tariff Policies
While cost-cutting is a reactive response, many companies also proactively engage in lobbying and advocacy efforts.
Engaging with Government Agencies:
Many businesses engage in lobbying efforts to influence tariff policies.
- Industry Associations: Groups representing various industries actively lobby government agencies to advocate for changes to tariff policies.
- Challenges: Influencing government decisions is a complex and often lengthy process, requiring considerable resources and expertise.
Seeking Tariff Exemptions or Modifications:
Companies also pursue tariff exemptions or modifications to reduce the impact of tariffs on their specific products or operations.
- Application Process: The process of applying for exemptions or modifications is often complex and involves detailed documentation.
- Success Rates: The success rate of obtaining exemptions or modifications varies significantly, depending on the specifics of the case and the prevailing political climate.
- Navigating Trade Regulations: Understanding and navigating the intricacies of international trade regulations is crucial for success in seeking these exemptions.
Conclusion
In response to tariff uncertainty, U.S. companies are primarily focusing on implementing comprehensive cost-cutting strategies. This involves restructuring supply chains, optimizing operations, and implementing strategic workforce adjustments. While lobbying efforts are underway, the immediate focus remains on mitigating the financial impact of fluctuating tariffs. The long-term implications for the U.S. economy remain to be seen, but the current trend strongly suggests a continued emphasis on cost efficiency and supply chain resilience.
Understanding and proactively addressing tariff uncertainty is crucial for long-term business success. Explore our resources to develop a comprehensive cost-cutting strategy tailored to your specific needs, and learn more about effective supply chain management in volatile markets.
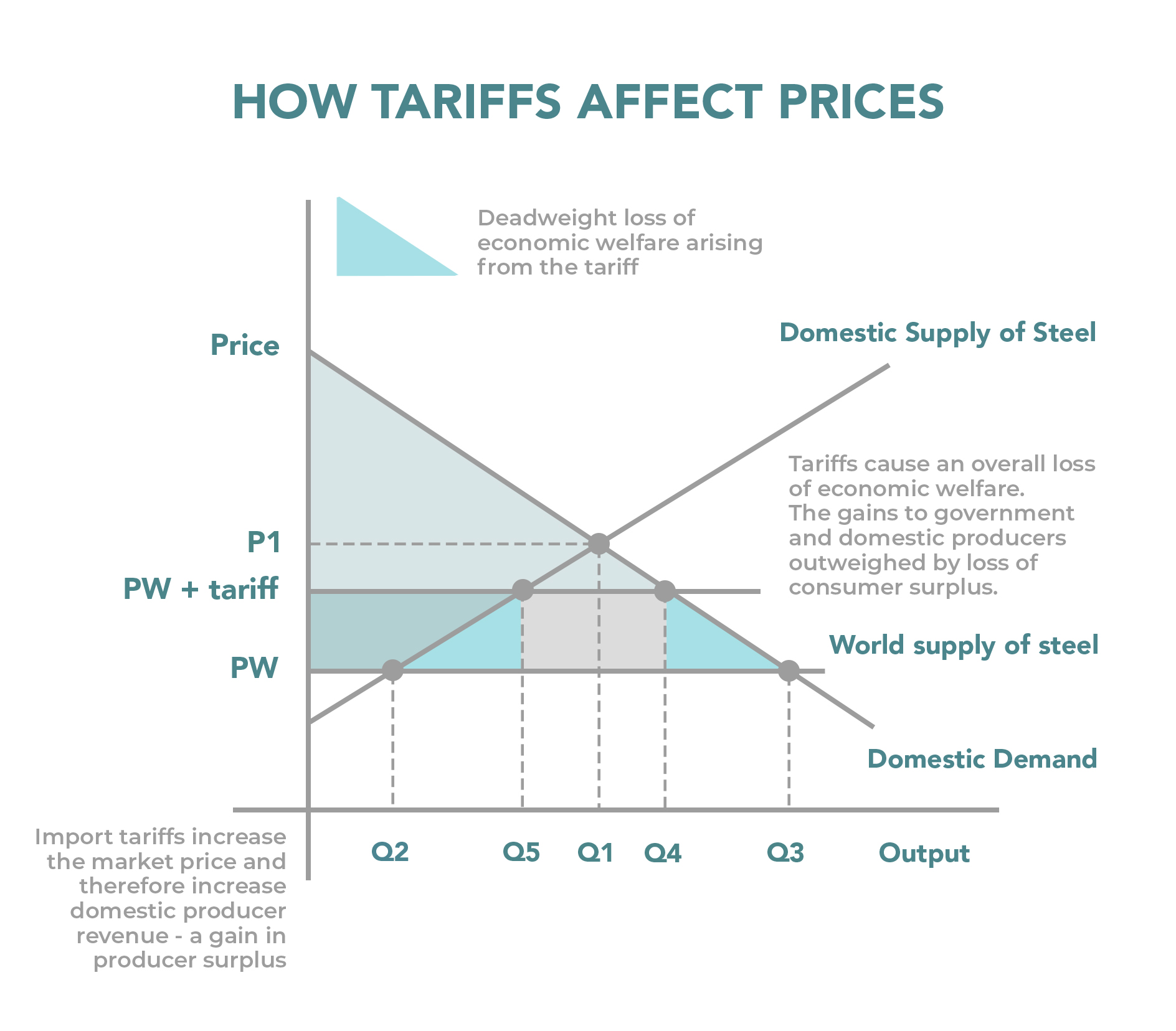
Featured Posts
-
Louisvilles River Road Construction A Crisis For Local Businesses
Apr 29, 2025 -
Analyzing Mhairi Blacks Claims Misogyny And The Protection Of Women And Girls
Apr 29, 2025 -
Black Hawk Helicopter Crash Nyt Details Pilots Alleged Disobedience
Apr 29, 2025 -
Kitzbuehel Tgi Ag Feiert Meilenstein Und Zukuenftige Plaene
Apr 29, 2025 -
Trumps Transgender Sports Ban Us Attorney General Targets Minnesota
Apr 29, 2025
Latest Posts
-
The Complex Relationship Between Misogyny And Womens Safety Insights From Mhairi Black
Apr 29, 2025 -
Analyzing Mhairi Blacks Claims Misogyny And The Protection Of Women And Girls
Apr 29, 2025 -
The Role Of Misogyny In Protecting Women And Girls A Critical Analysis With Mhairi Black
Apr 29, 2025 -
Mhairi Black On Misogyny And The Discourse Surrounding Womens Safety
Apr 29, 2025 -
Is Misogyny Underlying The Protection Of Women And Girls Mhairi Blacks Perspective
Apr 29, 2025