Overcoming Hurdles In Automated Lyophilized Vial Inspection
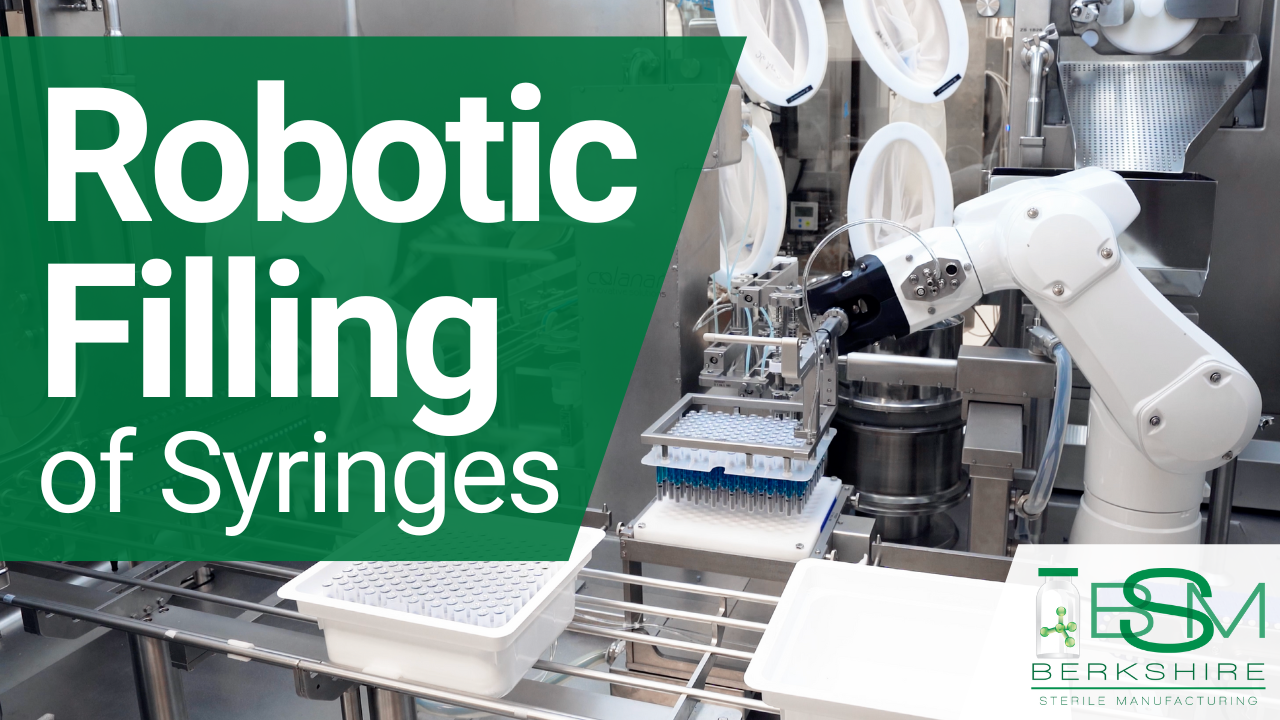
Table of Contents
Challenges in Implementing Automated Lyophilized Vial Inspection Systems
Implementing automated lyophilized vial inspection presents several significant hurdles that require careful consideration and strategic planning. These challenges span image processing, accuracy, and integration with existing workflows.
Image Acquisition and Processing Difficulties
Automated lyophilized vial inspection relies heavily on accurate image acquisition and sophisticated image processing algorithms. Variations in vial fill levels, stopper positioning, and the presence of subtle visual defects complicate automated image analysis. These variations can lead to inaccurate results and inconsistencies.
- Low contrast images: Variations in lighting and vial contents can create images with poor contrast, making defect detection difficult.
- Uneven lighting: Inconsistent illumination across the vial's surface can lead to false positives or negatives.
- Reflections: Glare and reflections from the vial surface can obscure defects and interfere with accurate measurements.
- Subtle particulate matter detection: Identifying small particles or other minute imperfections requires high-resolution imaging and advanced algorithms.
Solutions: Addressing these issues requires advanced image processing algorithms capable of handling variations in lighting and contrast. Specialized lighting techniques, such as structured illumination, can improve image quality. Furthermore, investing in high-resolution cameras with improved sensitivity can significantly enhance the accuracy of automated lyophilized vial inspection.
False Positive/Negative Rates
A critical concern in automated lyophilized vial inspection is the rate of false positives (rejecting good vials) and false negatives (accepting defective vials). Both scenarios have significant implications.
- Economic consequences of false positives: Rejecting good vials leads to wasted product, increased production costs, and reduced throughput.
- Safety risks of false negatives: Accepting defective vials poses serious safety risks to patients.
- The need for high accuracy: The system must achieve a high degree of accuracy to minimize both false positives and false negatives.
Solutions: Minimizing these errors requires sophisticated machine learning algorithms capable of learning and adapting to variations in vial appearance. Rigorous calibration procedures and regular system validation are crucial for maintaining accuracy. Implementing statistical process control (SPC) techniques helps to monitor the performance of the automated lyophilized vial inspection system and identify potential issues proactively.
Integration with Existing Production Lines
Integrating automated inspection systems into existing manufacturing processes can be complex and disruptive.
- Space constraints: Finding suitable space for the new equipment within an existing facility can be challenging.
- Compatibility with existing equipment: The automated system must be compatible with upstream and downstream equipment.
- Process downtime during integration: Integration requires careful planning to minimize downtime and maintain production schedules.
- Validation requirements: Rigorous validation is necessary to ensure the automated system meets regulatory requirements (e.g., GMP).
Solutions: Modular system designs can facilitate easier integration into existing production lines. Thorough planning, including a detailed risk assessment and comprehensive validation plan, is crucial for a smooth and efficient integration process. Engaging experienced system integrators can minimize disruption and ensure compatibility.
Strategies for Successful Automated Lyophilized Vial Inspection
Successfully implementing automated lyophilized vial inspection requires a multi-faceted approach that addresses system selection, parameter optimization, and robust quality control procedures.
Selecting the Right Inspection System
Choosing the right automated lyophilized vial inspection system is a critical first step. Several factors must be considered.
- Throughput: The system must meet the required production capacity.
- Accuracy: The system must meet the required accuracy and precision for defect detection.
- Flexibility: The system should be adaptable to different vial types and sizes.
- Cost: The initial investment and ongoing operational costs must be considered.
- Specific features: The system must include the necessary features, such as particle detection, fill level measurement, and stopper verification.
- Vendor selection: Choosing a reputable vendor with experience and a strong track record is important.
- Regulatory compliance: The system must comply with all relevant regulatory guidelines.
Optimizing Inspection Parameters
Careful adjustment of system settings is critical for optimal performance.
- Calibration techniques: Regular calibration ensures consistent and accurate measurements.
- Algorithm optimization: Fine-tuning algorithms can improve defect detection accuracy.
- Regular performance monitoring: Continuous monitoring allows for early detection of potential problems.
- Data analysis: Analyzing inspection data can identify trends and optimize system settings.
Implementing Robust Quality Control Procedures
Robust quality control procedures are essential for ensuring the accuracy and reliability of the inspection process.
- Regular system maintenance: Regular maintenance prevents malfunctions and ensures optimal performance.
- Operator training: Well-trained operators are crucial for proper system operation and troubleshooting.
- Data logging and analysis: Detailed data logging facilitates trend analysis and continuous improvement.
- Compliance with regulatory guidelines: Adherence to GMP and other relevant guidelines is paramount.
Conclusion
Successfully implementing automated lyophilized vial inspection systems requires careful planning, robust system selection, and rigorous quality control. By addressing the challenges outlined above and adopting the suggested strategies, pharmaceutical manufacturers can significantly improve product quality, enhance efficiency, and minimize risks associated with manual inspection methods. Investing in effective automated lyophilized vial inspection ensures patient safety and compliance with industry regulations. Don't compromise on quality – optimize your processes with the right automated lyophilized vial inspection solution today!
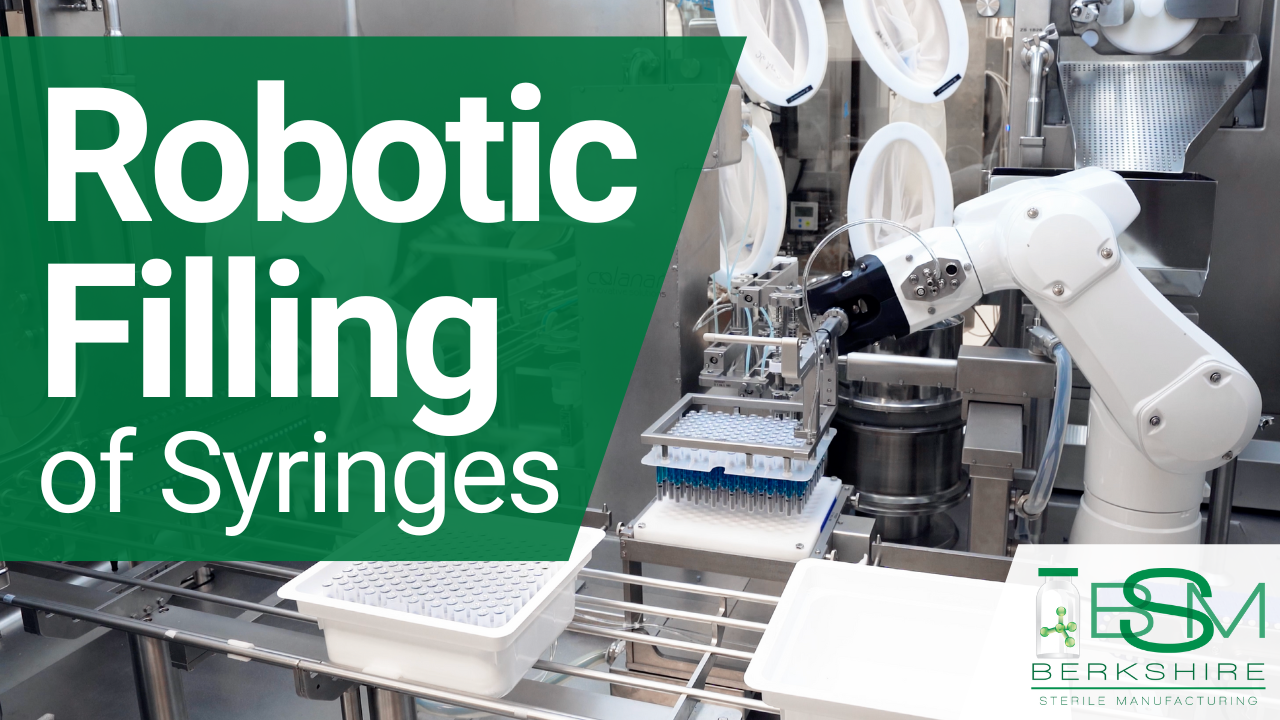
Featured Posts
-
Ufc 315 Predictions Belal Muhammad Vs Jack Della Maddalena Fight Pick And Odds Analysis
May 11, 2025 -
Kontrowersyjne Wyznania Masazystki Ksiaze Andrzej Bez Ubran
May 11, 2025 -
Karlyn Pickens Record Breaking 78 2 Mph Pitch A New Era In Ncaa Softball
May 11, 2025 -
John Wick 5 Confirmation And What We Know
May 11, 2025 -
Virginia Giuffres Claim 4 Days To Live Prince Andrew Allegations
May 11, 2025
Latest Posts
-
Lowry Challenges For Victory At The Valspar Championship
May 12, 2025 -
Boris Dzhonson Kritikuet Mirniy Plan Trampa Analiz Situatsii
May 12, 2025 -
Valspar Championship Lowry Makes A Push For The Title
May 12, 2025 -
Voyna V Ukraine Dzhonson Osuzhdaet Mirniy Plan Trampa
May 12, 2025 -
Reaccion De Boris Johnson Ante Ataque De Avestruz En Texas
May 12, 2025