The Future Of Automated Visual Inspection For Lyophilized Pharmaceutical Products
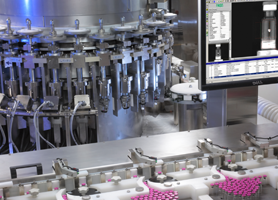
Table of Contents
Enhanced Speed and Efficiency in Lyophilized Product Inspection
Automated visual inspection systems provide a significant leap forward in the speed and efficiency of lyophilized product examination. This translates to substantial cost savings and enhanced production capacity.
Increased Throughput
AVI systems can process significantly more vials per hour compared to manual inspection, dramatically reducing production bottlenecks and accelerating time to market. This increased throughput offers several key advantages:
- Reduced inspection time translates directly to cost savings. Faster processing means lower labor costs and reduced operational expenses.
- Faster inspection allows for quicker identification and removal of defective products, minimizing waste. Defective vials are swiftly identified and removed from the production line, preventing further processing of substandard products.
- Increased capacity accommodates growing production demands without scaling up manual labor. This is particularly crucial in a rapidly expanding pharmaceutical market. AVI systems provide the scalability needed to handle increased production volume without a corresponding increase in human resources.
24/7 Operation & Reduced Labor Costs
Unlike human inspectors, automated systems operate continuously, maximizing production uptime and minimizing labor costs associated with shift patterns and overtime. The benefits extend beyond simple cost reduction:
- Consistent inspection quality is maintained regardless of time of day. Automated systems provide consistent performance, eliminating variability linked to human fatigue or varying levels of attention.
- Reduces reliance on human resources, addressing labor shortages in the pharmaceutical industry. AVI systems alleviate pressure on finding and retaining skilled human inspectors, a significant challenge in many regions.
- Frees up human inspectors for more complex tasks requiring specialized skills. Instead of repetitive visual inspection, human inspectors can focus on more complex tasks that require expertise and judgment.
Improved Accuracy and Reduced Human Error in Lyophilized Vial Inspection
Human error is an inherent limitation of manual visual inspection. Automated visual inspection significantly minimizes this risk, leading to higher accuracy and improved product quality.
Objective and Consistent Defect Detection
AVI systems utilize advanced imaging techniques, such as high-resolution cameras, spectral imaging, and even AI-powered image analysis, to detect subtle defects invisible to the naked eye. This ensures consistent and objective quality control:
- Minimizes the risk of human error in identifying cracks, particulate matter, or other imperfections. Automated systems can consistently identify even microscopic defects that might be missed by a human inspector.
- Provides detailed documentation of detected defects, facilitating root cause analysis and process improvement. The detailed data generated by AVI systems allows for in-depth analysis of defect patterns, pinpointing areas for process optimization.
- Enhances compliance with stringent regulatory requirements. The high level of accuracy and detailed documentation provided by AVI systems helps ensure full compliance with regulatory standards.
Data Analytics and Process Optimization
Automated systems generate comprehensive data on defect rates, trends, and patterns. This valuable data enables proactive process optimization and improved product quality:
- Predictive modeling can anticipate potential quality issues, preventing costly recalls. By analyzing defect trends, AVI systems can help predict and prevent future quality problems.
- Data-driven insights lead to more efficient manufacturing processes. The data generated allows for targeted improvements in the manufacturing process to minimize defects.
- Improved quality control reduces waste and enhances product reliability. By identifying and removing defective products early in the process, AVI systems minimize waste and ensure only high-quality products reach the market.
Future Trends in AVI for Lyophilized Pharmaceuticals
The field of automated visual inspection is constantly evolving, driven by advancements in artificial intelligence and imaging technologies.
Artificial Intelligence (AI) and Machine Learning (ML) Integration
The integration of AI and ML will significantly enhance the capabilities of AVI systems, leading to more accurate and adaptive defect detection:
- AI-powered systems can learn and adapt to variations in product appearance and defect types. AI algorithms can be trained to recognize a wide range of defects, even those not previously encountered.
- Improved algorithms will enable the detection of increasingly subtle defects. AI can improve the sensitivity of detection, identifying even the smallest imperfections.
- AI can assist in the automation of complex decision-making processes. This allows for more sophisticated analysis and interpretation of inspection results.
Advanced Imaging Techniques
The development and implementation of advanced imaging modalities, such as hyperspectral imaging and 3D imaging, will further enhance the accuracy and capabilities of AVI:
- Hyperspectral imaging provides detailed spectral information about the product, aiding in the detection of hidden defects. This allows for a more comprehensive analysis of the product's composition and identification of subtle defects that might be missed by traditional imaging techniques.
- 3D imaging allows for comprehensive analysis of vial geometry and content. This provides a more complete picture of the product, allowing for the identification of defects related to vial shape, fill level, and other three-dimensional aspects.
- Advanced imaging techniques can improve the detection of container closure integrity issues. This is crucial for ensuring the sterility and stability of lyophilized products.
Conclusion
The adoption of Automated Visual Inspection (AVI) of Lyophilized Products is no longer a matter of convenience but a necessity for maintaining high product quality, meeting stringent regulatory standards, and gaining a competitive edge in the pharmaceutical industry. The benefits of increased speed and efficiency, improved accuracy, and the incorporation of AI and advanced imaging technologies are undeniable. By embracing automated visual inspection solutions, pharmaceutical manufacturers can significantly enhance their quality control processes, reduce costs, and ensure the delivery of safe and effective lyophilized medications to patients worldwide. Invest in the future of pharmaceutical quality control—explore the possibilities of AVI for your lyophilized products today.
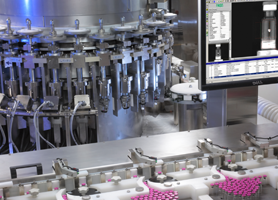
Featured Posts
-
Tam Krwz Awr An Ky Nyy Grl Frynd Hqyqt Ya Afwah
May 12, 2025 -
Adele Lim To Develop Crazy Rich Asians Series For Hbo Max
May 12, 2025 -
Knicks Vs Pistons Betting Odds And Predictions Activate Bet365 Bonus Code Nypbet
May 12, 2025 -
Bkfc Fight Conor Mc Gregors Jose Aldo Inspired Moment
May 12, 2025 -
Chantal Ladesou Critique Ouvertement Ines Reg Elle Aime Le Conflit
May 12, 2025
Latest Posts
-
Parliamentary Pressure Mounts Action Needed On Undocumented Workers
May 12, 2025 -
Netherlands Extends Border Checks Despite Fewer Arrests And Asylum Claims
May 12, 2025 -
Legal Action Marjolein Faber And The Misuse Of Her Image At A Demonstration
May 12, 2025 -
Asylpolitik Beratungsgremien Fordern Bessere Organisation Und Kostenersparnis
May 12, 2025 -
Optimierung Von Asylunterkuenften Einsparungspotenzial Von Einer Milliarde Euro
May 12, 2025