U.S. Businesses Implement Cost-Cutting Strategies In Response To Tariffs
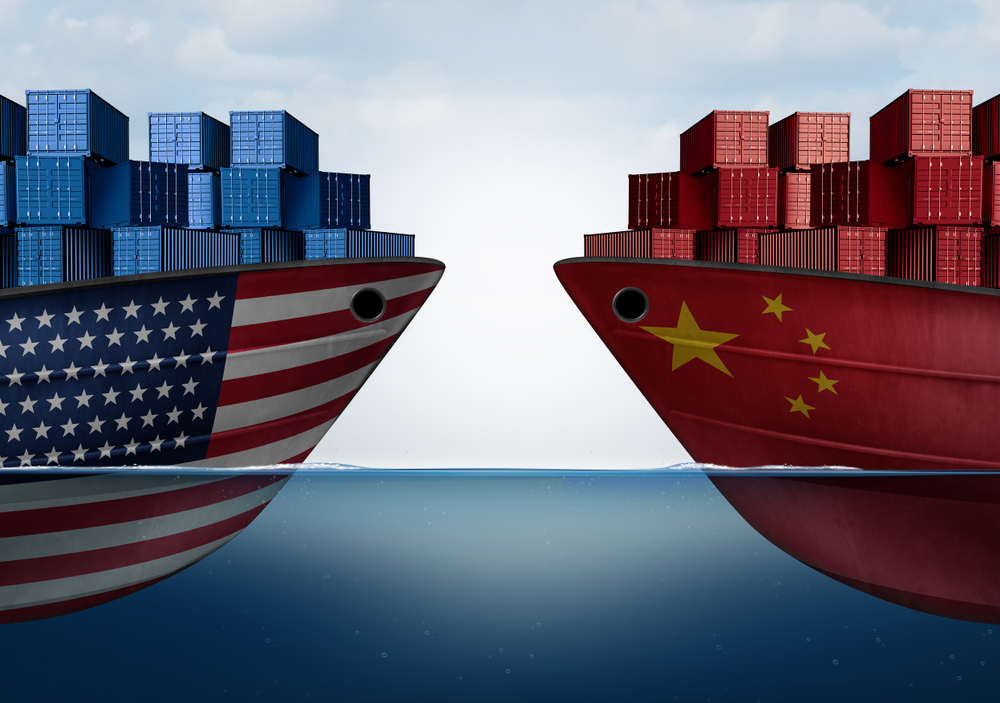
Table of Contents
Restructuring Supply Chains to Minimize Tariff Impacts
One of the most significant responses to rising tariffs has been the restructuring of supply chains. Businesses are actively diversifying their sourcing, moving away from countries heavily impacted by tariffs to minimize import costs. This involves several key strategies:
- Shifting Production: Many companies are shifting production to countries with more favorable trade agreements or lower tariff rates. This might involve relocating manufacturing facilities or establishing partnerships with manufacturers in alternative locations.
- Nearshoring and Reshoring: Nearshoring (moving production to nearby countries) and reshoring (bringing production back to the U.S.) are gaining traction. This reduces transportation costs, lead times, and tariff burdens associated with long-distance shipping.
- Import Diversification: Businesses are diversifying their import sources, reducing reliance on single suppliers or countries. This spreads risk and makes them less vulnerable to disruptions from specific tariff policies.
- Investing in Automation: To offset increased labor costs or to reduce reliance on specific regions, companies are investing heavily in automation technologies. This improves efficiency and reduces reliance on human labor in tariff-affected areas. This includes everything from robotic process automation to advanced manufacturing equipment.
Optimizing Production Processes for Enhanced Efficiency
Beyond supply chain adjustments, businesses are intensely focusing on optimizing their internal production processes to improve efficiency and reduce costs. This involves:
- Lean Manufacturing Principles: Implementing lean manufacturing principles helps minimize waste in materials, time, and resources, thereby lowering overall production costs. This includes techniques like Kaizen (continuous improvement) and Six Sigma.
- Technological Upgrades: Investing in advanced technologies, such as automation, robotics, and data analytics, can significantly enhance productivity and reduce labor costs. This also includes software solutions for inventory management and process optimization.
- Inventory Management: Optimizing inventory management reduces storage costs, minimizes waste from spoilage or obsolescence, and improves cash flow. Utilizing Just-in-Time (JIT) inventory systems can significantly reduce these expenses.
- Energy Efficiency: Improving energy efficiency through upgrades to equipment and processes can result in substantial savings on utility bills, contributing to overall cost reduction.
Negotiating with Suppliers and Reducing Operational Expenses
Negotiating favorable terms with suppliers and reducing operational expenses are crucial aspects of the cost-cutting strategies being employed. Strategies include:
- Contract Renegotiation: Businesses are renegotiating contracts with existing suppliers to secure lower prices or more favorable payment terms. This often involves leveraging market conditions and demonstrating the mutual benefits of a long-term partnership.
- Consolidated Purchases: Consolidating purchases to leverage bulk discounts provides significant cost savings on materials and supplies. This often involves strategically planning purchases to take advantage of volume-based pricing.
- Alternative Materials: Exploring alternative, less expensive materials without compromising quality is a key strategy for cost reduction. This requires careful evaluation of material properties and supplier reliability.
- Expense Reduction: Streamlining administrative processes and reducing overhead costs through process improvement initiatives helps to free up resources and improve operational efficiency.
Leveraging Government Resources and Support Programs
The U.S. government offers several resources and support programs designed to help businesses cope with the challenges posed by tariffs. These include:
- Trade Relief Programs: Businesses can apply for trade relief programs, such as tariff exclusions or countervailing duties, to offset the impact of tariffs. Understanding eligibility requirements and navigating the application process is crucial.
- Tax Incentives and Subsidies: Several tax incentives and subsidies are available to businesses that invest in domestic manufacturing, research and development, or job creation. These programs can significantly reduce the overall cost burden.
- Small Business Support Programs: Small businesses can access a variety of support programs, including grants, loans, and technical assistance, to help them navigate the challenges posed by tariffs. These programs are often administered at the state or local level.
- Trade Organization Resources: Numerous trade organizations and government agencies provide resources and guidance to businesses affected by tariffs. These resources can provide valuable insights, support, and networking opportunities.
Conclusion
U.S. businesses facing the challenges of tariffs are demonstrating remarkable resilience by employing a combination of cost-cutting measures. From restructuring supply chains and optimizing production processes to negotiating with suppliers and leveraging government resources, a multi-faceted approach is proving essential for survival and long-term success. Proactive adaptation is key to navigating this complex economic environment. To effectively mitigate the effects of tariffs and maintain profitability, businesses should thoroughly explore the cost-cutting strategies discussed and seek professional advice on implementing effective cost-cutting strategies in response to tariffs. Don't wait – take control of your business's future by adopting a comprehensive approach to tariff mitigation today.
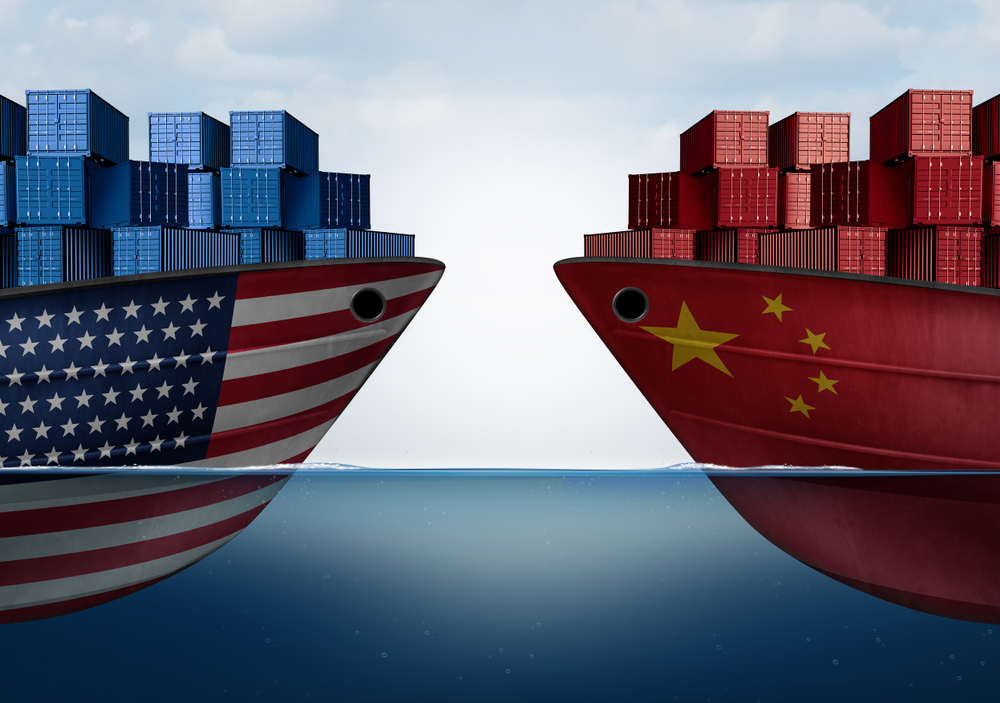
Featured Posts
-
Millions In Losses Inside The Office365 Executive Inbox Hacking Scheme
Apr 29, 2025 -
Open Ai Facing Ftc Investigation Analyzing The Potential Consequences For Chat Gpt And The Ai Industry
Apr 29, 2025 -
The Rise Of Wildfire Betting Los Angeles And The Ethics Of Disaster Gambling
Apr 29, 2025 -
Humanitarian Crisis In Gaza Urgent Need For Israel To Lift Aid Restrictions
Apr 29, 2025 -
Analyzing The Effectiveness Of Minnesotas Film Tax Credit Program
Apr 29, 2025
Latest Posts
-
Austin City Limits Willie Nelson And Family Concert Details And Tickets
Apr 29, 2025 -
Experience Willie Nelson And Family Live At Austin City Limits
Apr 29, 2025 -
Teslas Strength Tech Rally Lift Us Stocks Higher
Apr 29, 2025 -
Yukon Legislature Mine Managers Silence Sparks Contempt Threat
Apr 29, 2025 -
The U S Dollars Performance A 100 Day Comparison To The Nixon Era
Apr 29, 2025